Pre-shipment Inspection Service in Türkiye
Ensure Quality Before Delivery with QCmatic’s Pre-Shipment Inspection
Pre-Shipment Inspection Service
We understand that the final steps before shipment are crucial to ensuring the quality and integrity of your products. Our pre-shipment inspection service is designed to verify that your products meet all specified requirements and standards before they leave the factory. With our meticulous approach and expert team, we help you avoid costly surprises and ensure customer satisfaction.
What is Pre-Shipment Inspection?
Pre-shipment inspection (PSI) is a quality control process conducted before goods are shipped to the customer. This critical step ensures that products are manufactured according to the specifications, standards, and requirements agreed upon. It involves thorough checking of product quality, quantity, packaging, and labeling to confirm that everything is in order before shipment.
Benefits of Pre-Shipment Inspection
- Quality Assurance: Verify that products meet specified quality standards and customer requirements.
- Risk Mitigation: Identify and address any issues before products are shipped, reducing the risk of returns and complaints.
- Cost Savings: Avoid costly rework, replacements, and logistics expenses by catching defects early.
- Customer Satisfaction: Ensure that customers receive high-quality products, leading to increased trust and repeat business.
- Compliance: Confirm that products comply with relevant regulations and standards, avoiding legal and financial penalties.
Our Pre-Shipment Inspection Process
At QCmatic, our pre-shipment inspection process is comprehensive and tailored to meet the unique needs of each client. Our process includes:
- Preparation: We work with you to understand your specific requirements, product specifications, and inspection criteria.
- Requirement Analysis: We review the purchase order, technical specifications, quality standards, and other relevant documents.
- Inspection Plan Development: We develop a detailed inspection plan outlining the scope, criteria, sampling methods, and timeline for the inspection.
- On-Site Inspection: Our skilled inspectors visit the manufacturing site to perform a detailed examination of the products. This includes:
- Visual Inspection: Checking for defects, damages, and overall appearance.
- Surface Defects: Scratches, dents, discoloration, and other visible imperfections.
- Assembly Quality: Proper assembly, alignment, and finish of parts and components.
- Functionality Testing: Ensuring that products function as intended.
- Operational Checks: Testing moving parts, electronic functions, and other operational aspects.
- Performance Tests: Verifying that the product performs according to specified parameters.
- Measurement Verification: Confirming that dimensions and specifications match the requirements.
- Dimensional Checks: Measuring critical dimensions using precise instruments.
- Tolerance Verification: Ensuring that measurements fall within specified tolerances.
- Quantity Verification: Counting and confirming the number of units.
- Full Count: Verifying the total quantity of products to be shipped.
- Batch Consistency: Ensuring that batch numbers and production lots are consistent.
- Packaging Inspection: Checking packaging integrity, labeling, and compliance with shipping standards.
- Packaging Materials: Verifying the quality and suitability of packaging materials.
- Labeling: Ensuring labels are accurate, clear, and compliant with regulations.
- Sealing and Security: Confirming that packages are sealed correctly and secure for transport.
- Visual Inspection: Checking for defects, damages, and overall appearance.
- Sampling: Selecting random samples for detailed inspection to provide an accurate representation of the entire batch.
- Random Sampling: Using statistically valid sampling methods to select representative samples.
- Detailed Analysis: Conducting in-depth inspections on selected samples to identify any potential issues.
- Reporting: Providing a detailed inspection report with findings, including photographs, measurements, and recommendations.
- Comprehensive Documentation: Detailing all aspects of the inspection process, findings, and any deviations from standards.
- Photographic Evidence: Including high-resolution photos of inspected items and any identified issues.
- Recommendations: Offering clear guidance on any corrective actions needed to address issues.
- Feedback and Corrective Actions: Working with you to address any identified issues and ensure corrective actions are taken before shipment.
- Client Consultation: Discussing inspection findings with you and providing expert advice on next steps.
- Corrective Action Plan: Developing a plan to address any non-conformities and ensure compliance.
- Follow-Up Inspections: Conducting re-inspections if necessary to verify that corrective actions have been implemented effectively.
Why Choose QCmatic for Pre-Shipment Inspection?
- Expertise: Our team of experienced inspectors has extensive knowledge across various industries, ensuring thorough and accurate inspections.
- Advanced Technology: We use state-of-the-art tools and techniques to provide precise and reliable inspection results.
- Customization: Our inspection services are tailored to meet your specific requirements and industry standards.
- Timeliness: We understand the importance of deadlines and ensure timely inspections to keep your supply chain on track.
- Reliability: Trust QCmatic to deliver consistent and dependable inspection services that safeguard your business interests.
Industries We Serve
We cater to a diverse range of industries, including:
- Manufacturing
- Automotive
- Aerospace
- Machinery
- Medical Equipment
- Petrochemicals
- Construction
- Energy
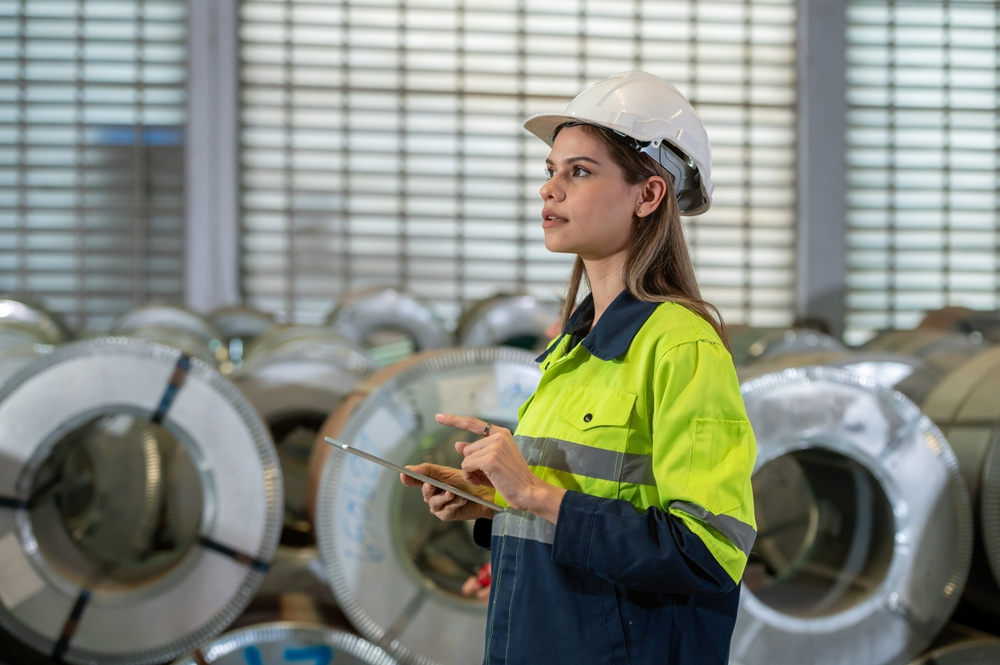